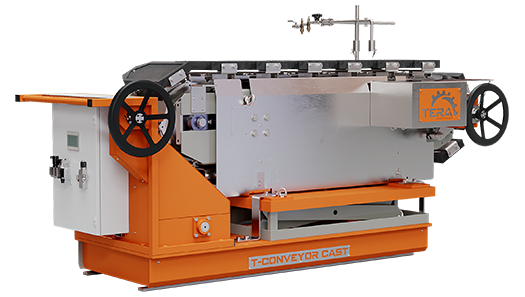
T-CONVEYOR CAST
AUTOMATIC INGOT CASTING MACHINE TO PRODUCE PRECIOUS AND NON-FERROUS METAL ANODES AND BARS
T-Conveyor Cast™ is a system designed for companies casting anodes and bars in precious and non-precious metal. As a matter of fact, this ingot casting machine can be combined to tilting melting furnaces with both vertical and horizontal casting, working with different types of molten metal: gold, silver, copper, brass, zinc, aluminum, etc.
We designed it specifically to lighten the burden of operators' manual workload - just think of the heavy weight of cast iron ingot molds alone - and to drastically reduce risks at work due to the proximity to furnaces. This is made possible by using a pushbutton panel (also available in a wireless version), which allows operating tasks at a safe distance.
Once you add the T-Conveyor Cast™ to your company's production flow, you will immediately perceive how much the pace of production of anodes and bars increases.
ADVANTAGES
THE BENEFITS OF AN INNOVATIVE, AUTOMATED SOLUTION:
01
Safety
Minimising direct contact with the furnaces thanks to the push-button panel, also wireless, which allows remote operations, improving operating conditions and reducing risks.
02
Efficiency
Incremento significativo della produzione oraria di anodi e barre, ottimizzando tempi e costi.
03
Versatility
Compatible with tilting melting furnaces and suitable for horizontal and vertical casting of various metals (gold, silver, copper, brass, zinc, aluminium, etc.).
04
Ergonomics
Eases the operator's physical workload by independently handling the heavy weight of cast iron ingot moulds.
MODELS
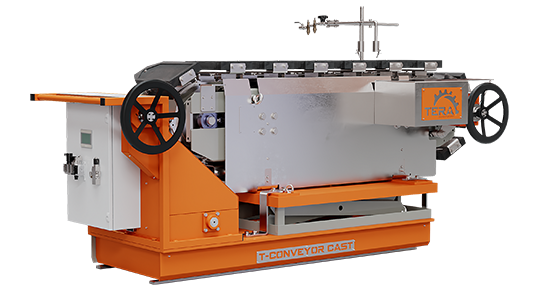
Dimensions | 3050 x 900 x h1450 mm |
Weight | 2000 kg |
Max. absorbed power | 4,5 kW |
Max number of molds | 16 standard / 32 slim |
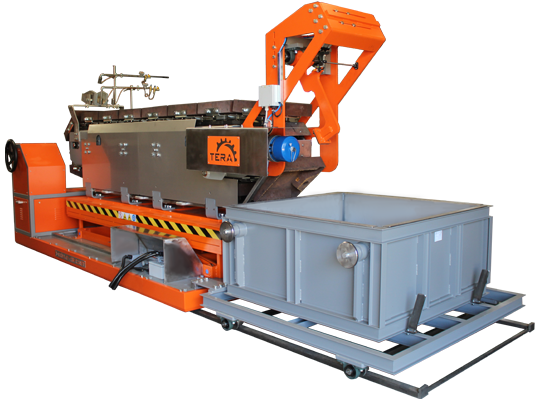
Dimensions with closed pantrograph | 5050 x 1850 x h2270 mm |
Dimensions with closed pantrograph | 5050 x 1850 x h3470 mm |
Weight | 2000 kg |
Max absorbed power | 7 kW |
Max number of molds | 32 standard / 48 slim |
TECHNOLOGY
HOW DOES T-CONVEYOR CAST™ MACHINE WORK?
01
Molten metal is poured from the melting furnace into the cast iron molds. The gradual pouring of the right quantity of molten metal inside the mold is controlled by the operator that manages the casting furnace.
02
Normally, the newly filled mold moves forward in synchronized steps, the next mold arrives in the casting position and the operator can discharge the molten metal. The molds containing the solidified metal bars gradually reach the unloading area.
03
The molds unloading is managed by a special mechanical striker, which can be operated manually by the operator automatically by remote control. The row of ingot molds runs continuously. Its movement can be operated in both directions and can be set both manually and automatically.