CHOOSE THE AUTOMATION LEVEL THAT BEST SUITS YOUR COMPANY
AUTOMATION FOR FLAWLESS INGOTS PRODUCTION
Each Tera Automation machine can be conceived as part of a modular line which can be combined according to the company's needs and facility space. Each machine can be fitted to existing machines and a full line can be developed over time.
The standard model of our T-Barmaster™ is semi-automatic, but it can reach a high level of automation. By adding accessories, machines and robots, operators can set the machine at increasing levels of automation and let it work accordingly:
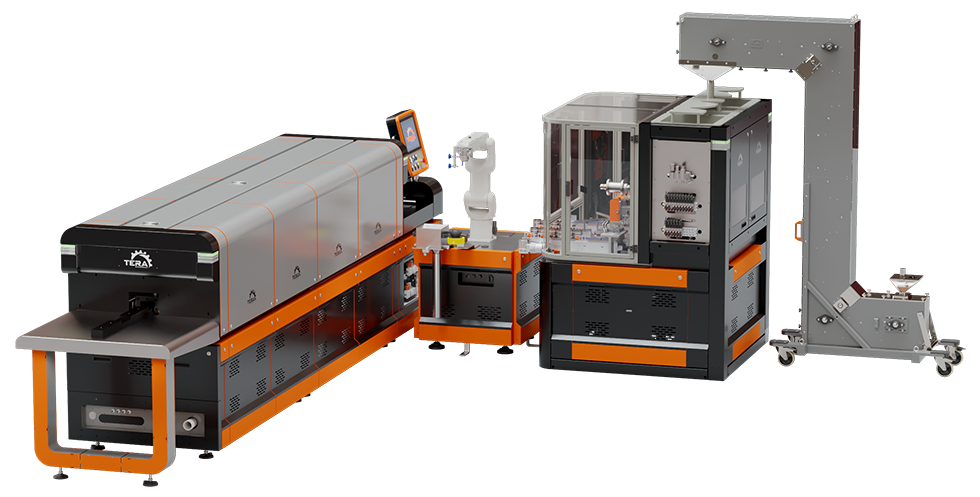