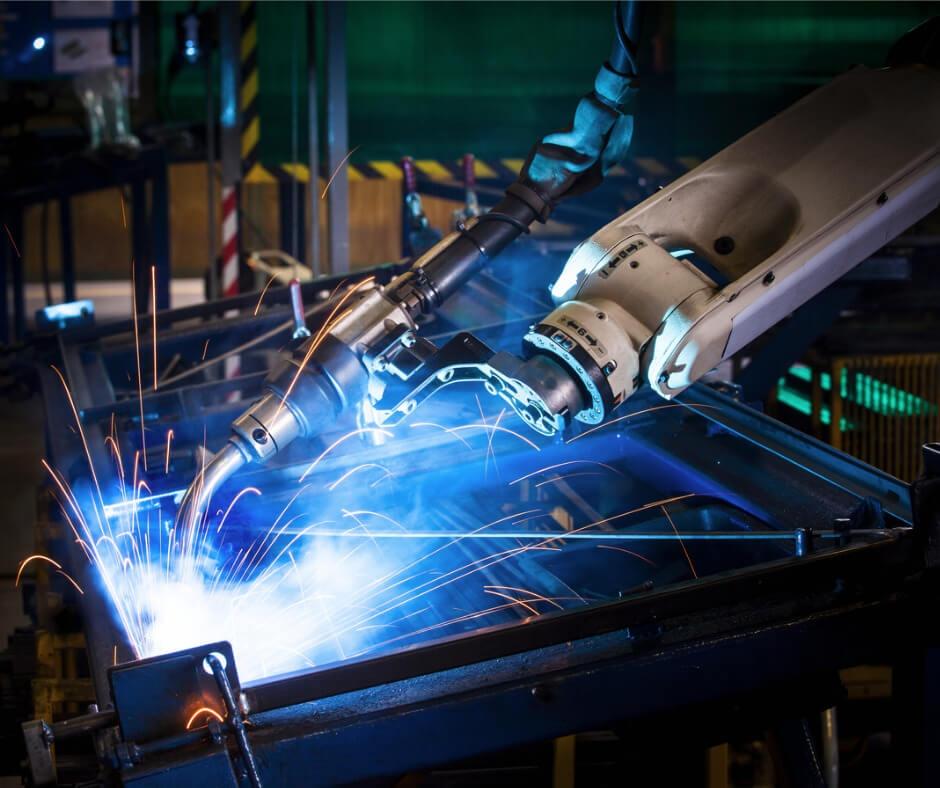
ROBOTIC CELLS FOR WELDING
Welding is an extremely demanding process, and today industrial robotics is making daily strides in the evolution of robots that can replace humans in a complex and risky task.
The use of industrial robots in welding tasks has been rather late in coming if we consider their massive use in the automotive field. While the first robots in America appeared in the 1960s for automotive production, welding robots waited until the 1980s to make their appearance in industrial production processes. But from this late start, they have since become the most widely used types of robots, especially in the US.
Robotic welding
Robotic welding is utilized in many industrial branches, but some stand out for the benefits drawn from the use of robotic cells intended for this process. In fact, they are used for welding phases in industrial processes in the automotive, furniture, household appliances, electrical panels and cabinets, hydraulic cylinders and carpentry sectors.
But what exactly does a robotic cell for welding do? It is commonly used in high production applications for a variety of welding types and materials.
The robotic cell can devote itself to welding:
- Electric arc
- Spot
- Oxyacetylene
- Resistance
- Concentrated energy
The robot designed to perform welding, can weld:
- Stainless steel
- Carbon steel
- Aluminum steel
- Titanium steel
- Alloy steels
It is therefore evident the extreme versatility of robotic cells for welding.
The automation of the welding process is made possible by the fact that it is a repetitive operation applied to similar objects and components. The industrial robot programmed to perform a specific type of welding on a specific metal will always perform it in the same way, maintaining the same level of precision and production times.
The robots used in robotic cells for welding usually have limited floor space inside the cell and are very fast in their movements. The primary objective, in fact, of their use is to reduce the execution time of an operation that requires particular attention from the operator.
In addition to increasing production speed, robotized welding maximizes the quality level of execution and safety at work. Manual welding, in fact, is quite risky for the operator, who must be equipped with certified PPE. The fusion of metal is made possible thanks to high temperatures and the danger of burns, even serious ones, is very high. Not to mention the risks to the eyes caused by electromagnetic radiation, or those arising from the accidental inhalation of dust, fumes and vapors.
It is obvious that a machine will not be exposed to these same risks. This would automatically lead to the choice of robotic welding, but let's compare it with traditional manual welding.
FIND OUT HOW MUCH A ROBOTIC CELL WOULD COST TO YOUR COMPANY WITH OUR ONLINE CONFIGURATOR
Manual welding vs robotized welding
Why choose robotic welding over manual welding?
Manual welding is part of many artisan professions and just as many industrial processes where the welding style must change at a very fast pace. The profession of welder is therefore a figure that will remain essential in many companies, but in some cases, it can be flanked by a robotic unit.
The latter actually provides many benefits, including:
- Extreme precision in welding execution without any loss of attention;
- Less probability of risks for the operator;
- Higher productivity on 24-hour shifts;
- Reduced waste and scrap because robotic welding is inherently more accurate;
- More flexibility: our robotized welding cells can be easily adapted to production changes by simply modifying a few components and reprogramming the robot positions;
- Reduced footprint: a single robotic station definitely takes up more space than a manual one, however, when dealing with large production runs, a cell with several robots can be concentrated in a limited size;
- Fast ROI: greater efficiency means greater speed and therefore also greater earnings and savings, especially for mass production.